A few names need no introduction: Jordan, Brady, Tyson. They are heavy hitters to say the least, and in the world of 3D printing, Stratasys is wearing the Golden Gloves. Founded in 1989, Stratasys has been in the game for 34 years, and they continue pushing the boundaries of what's possible with additive manufacturing. Luckily for us at AET Labs, we got to go hands-on with Stratasys' P3 technology, specifically with the Origin One 3D printer, to explore the workflow process firsthand.
What Exactly is P3 Technology?
The list of additive technology acronyms is ever-evolving, and P3 is here to stay because it stands for Programmable Photopolymerization. Try saying that five times fast, and you'll see why P3 sticks!
Photopolymerization is the process of a polymer changing its properties when exposed to light. Pretty simple, right? This is a relatively well-known and foundational process of many 3D printers on the market today ranging from hobbyist resin machines to the Stratasys Origin One.
Continue on to follow Nick Amos' initial experiences and experimentations with the Stratasys Origin One. Nick is AET Labs' Application Specialist, providing professional development training to instructors at New England schools and universities.
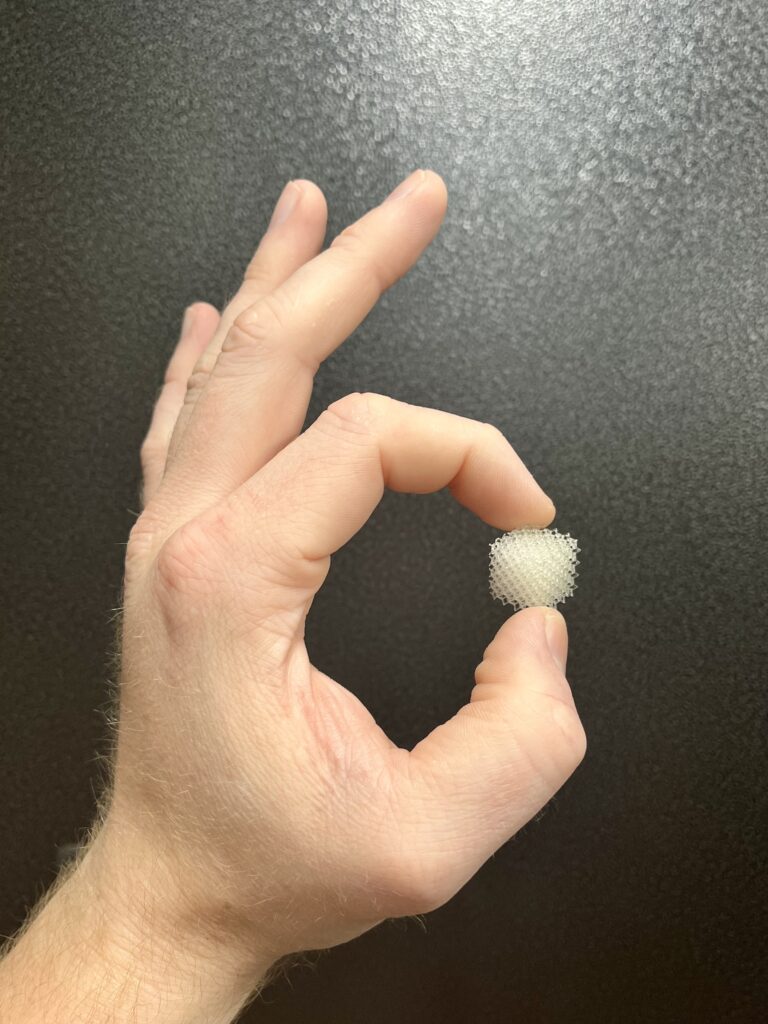
Get Crazy with Materials
Ok, so we're printing with light…magical,right? Actually, no. Scientifically, it's pretty straightforward. We're using a specific range of ultraviolet lightwaves, specifically those in the 385nm range, to initiate the photopolymerization. Why does this matter? Stratasys isn't the only one in the game, and this range of light is relatively universally used amongst the light-based printer community, both in machine design, software parameters, and materials.
However, Stratasys has its own ecosystem of materials, including all the "regulars" like basic, tough, high-temperature, elastic, etc. They also work with specific industry partners like Loctite, Henkel, and others to expand on certifiable materials. Setting standards for and working in collaboration with industry players is how they're contributing to a more open ecosystem. Plus, with other materials on the market, YOU have the ability to test and develop, win-win.

Wake Up!
Upon powering on the Origin One machine, I was greeted with an unnecessarily large green checkmark, and the machine's serial number proudly displayed on the tablet-sized screen. A touch anywhere woke the machine from this sleep-like state and brought me to the home screen. Menu tabs run down the left, variable buttons across the top, and the active window takes up the remaining 2/3rds of the screen's real estate. Stoplight colors subtly guided me, and I caught on right away. Everything is clear, legible, and high contrast, and most importantly, the user interface is intuitive. If you can operate a smartphone, you can handle this.
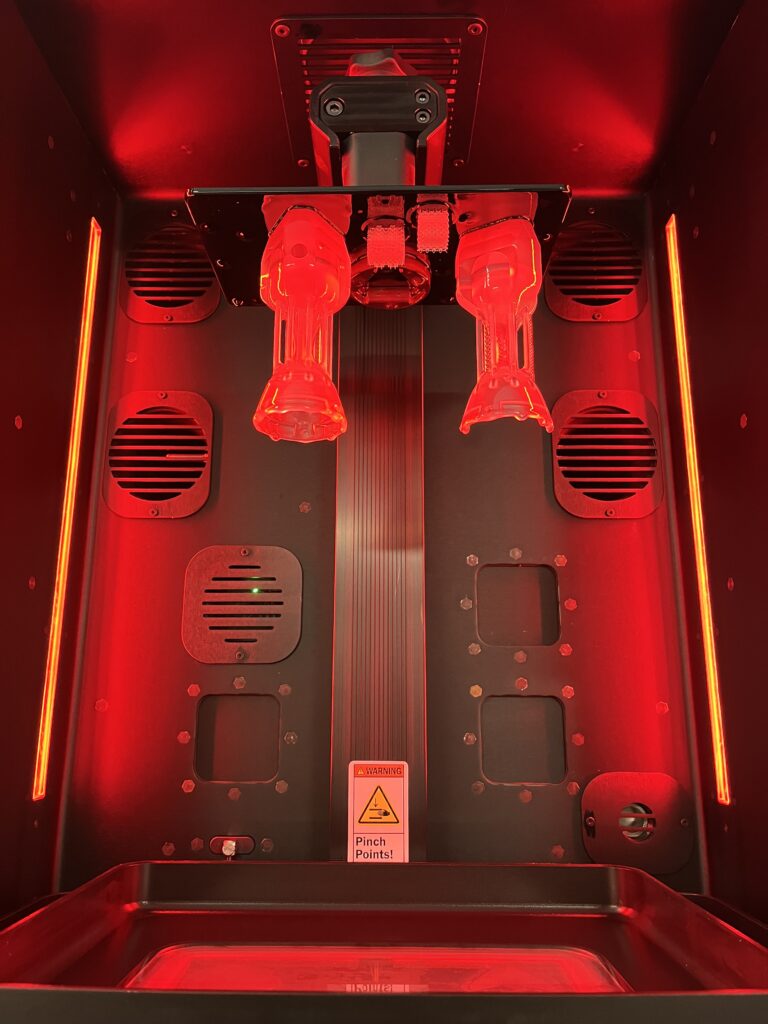
Home is Where the……Build Plate is Zero'd
As with every other machine, I needed to get started by ensuring the build plate was level and square. Selecting the prompt to do so brought on-screen images and text descriptions of each step, one at a time. It's hard to make mistakes when it's this simple, right?
This is a good time to mention this machine's size. The build plate is 8.6 inches when measured diagonally, like a television screen. Specifically, the build volume is 7.6" in the X axis, 4.25" in the Y, and has a pretty impressive 13.78" in Z. If you prefer MM or whole numbers, that's 192x108x350mm.
The process is simple. Loosen the large knob holding the build plate to the support arm and a single Allen-head screw to unlock the build plate's spherical flexibility. A small torque-adjustable Allen tool is provided to protect the longevity of this locking system. Even my gigantic hands can comfortably fit between the knob and enclosure ceiling. I sent the plate down once it was loose, allowed it to bottom out, held it steady, and snug it back up—simple as that! This is a relatively universal process, and the included tool is quite nice.
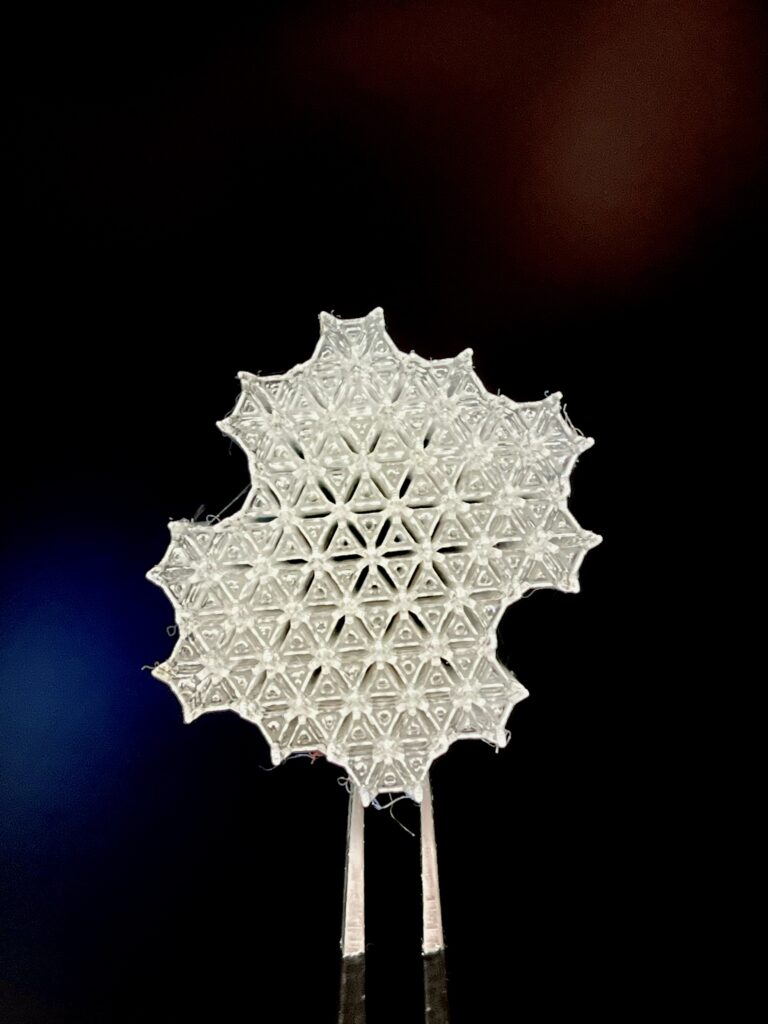
Shaken or Stirred?
Most, if not all, manufacturers recommend ensuring that your material is thoroughly mixed, but often don't provide guidelines. Shaking it up certainly mixes it well, but it can add lots of bubbles, which can impact your parts (ask me how I know…). Stirring it can work just as well, but it's just a slower process. Who's got time for that?
Generally speaking, your resin will also have a recommended temperature window. The printing process is exothermic in nature, giving off heat as it cures. This can cause variations in resin temperature throughout the duration of the print, which can be problematic. My workflow has always been to shake my resins vigorously, then soak them in a large bowl of scalding hot water for ten minutes. This gives the bubbles time to work their way out and the resin to come up to temp. Admittedly this needs to be more accurate.
The Origin One is a treat because its chamber and Vat are heated, monitored with infrared cameras, and managed digitally (up to 60C/140F). The temperature can be set manually from the menu, pour in your well-mixed resin, and let the machine do the work while you make your coffee! Features like this are incredibly user-friendly, plus all this data is at your disposal. You can quickly and easily access the analytics menu tab and monitor temperature over time, real-time camera imagery, and much more. Seriously, too much more. We'd have a thesis paper on our hands if we covered all the sensors.
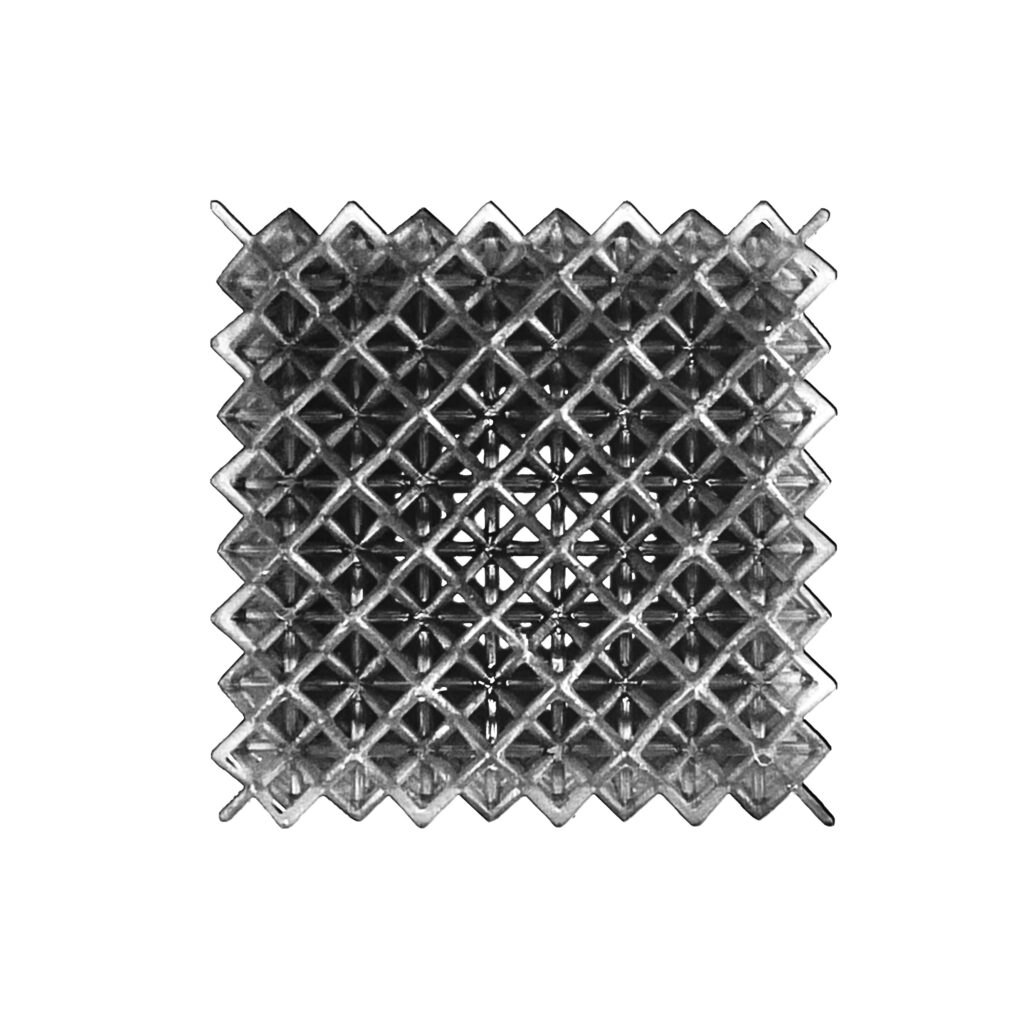
File Prep
We'll keep this one short and sweet. The Origin One is designed to work with GrabCAD Print, or its paid big brother, GrabCAD Print Pro. There is a myriad of slicers on the market for all different printer platforms. (If you've read this far, I'm sure you're familiar with one or two of them). GrabCAD print is immediately recognizable but generally an underwhelming experience when paired with the Origin One as support generation has to be done externally through Netfabb, a process in and of itself. This is kind of crazy for 2023, but support generation is being worked into the platform as we speak and will be available in a future software generation. The Pro version has some advanced and unique features, depending on which printer(s) it's being applied to.
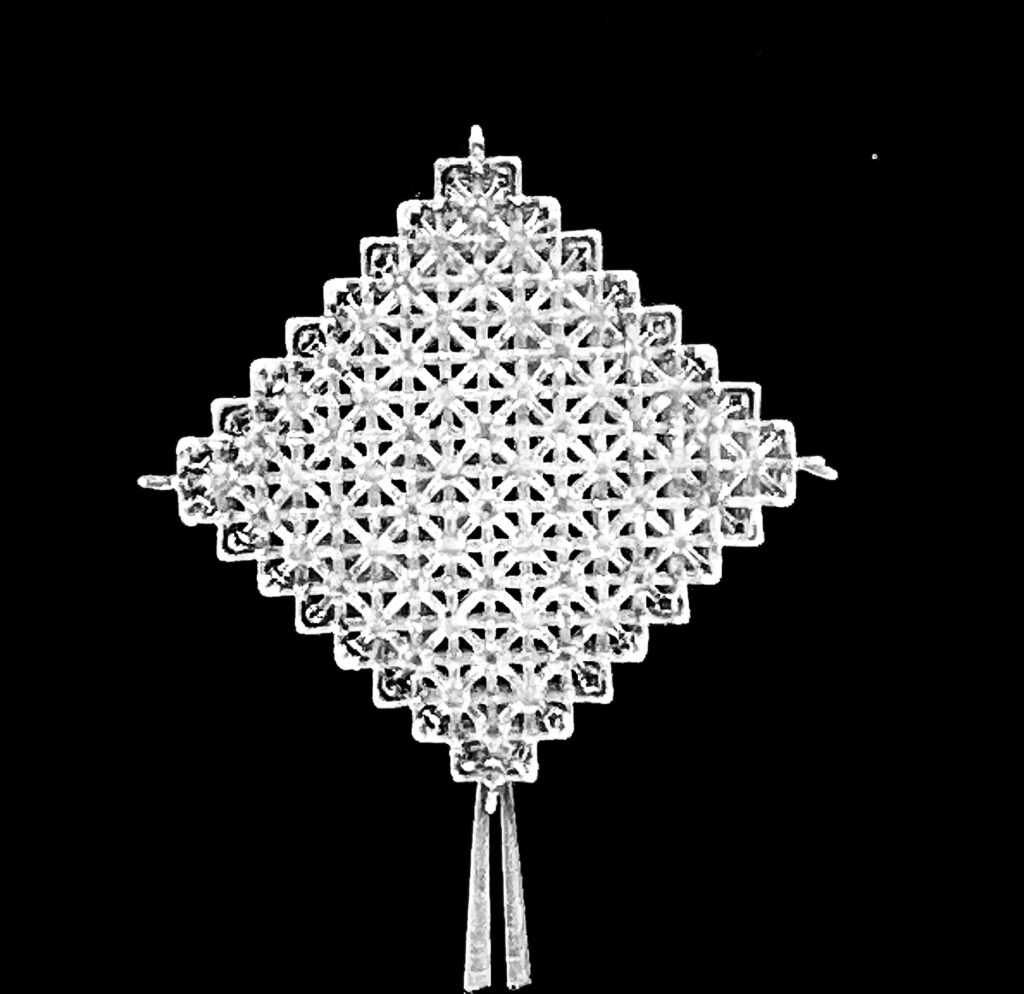
Standing Out, Pneumatically
Having quite a bit of experience under my belt with resin machines, most people I speak with seem to be firmly in the "Pro Support" camp. I, however, avoid supports like the plague. Wasted material, inevitable surface imperfections, more extensive pre and post-processing, innumerable settings to dial in, let me count the ways. Don't get me wrong, it can be quite a process attempting to avoid them too! Bed adhesion issues are abundant, part deformation, the ole' elephants' foot, and on and on. Truth be told, both mindsets have a home in the workflow, and at the end of the day, not every variable is in just one person's hands.
The Stratasys Origin One, though, has a very clever trick up its sleeve, and it absolutely SHINES when dealing with large surface area or flat-to-build plate-style printing. Using sensors again, the Origin One constantly monitors separation force during build plate retractions and manages it with a unique pneumatically controlled tray seal. Yes, you read that right. They've really captured my heart with this one!

Clean Up, Clean Up
That's likely not what you'll be humming to, but you'd be smart to put some tunes on in the background. As with all resin printers, when the part comes off the build plate, you aren't finished. After drip drying and separation, parts are cycled into a "dirty" IPA bath to remove the bulk of uncured resin stuck to their surface, then a "clean" IPA bath to remove the remaining resin, both inside a sonic tank. Still from here, some parts require a gentle scrubbing with a toothbrush aided by some more alcohol to rinse away the debris. Parts must be dried thoroughly to avoid surface droplets of IPA evaporating during the UV Bath and leaving visible "water spots." While things dry, you'll be emptying the Vat through a filter and funnel to preserve your supplies and cleaning the Vat thoroughly, unless more printing is queued up, of course!
For curing, I used a UV Flood System by Dymax, and a sonic tank by Branson, both preferred industry hardware. This stage of post-processing highlighted my only gripe with this machine, the Vat tray. I can appreciate the handles, as the weight is not unsubstantial, especially when filled with resin. But removing the tray from the machine's grip is an event, and draining the Vat is bound to make a resin mess of the handle and the impossible-to-clean gap between it and the tray.

A Warm Welcome
Tasked with demonstrating this machine, I set out to push its boundaries. Pushing them in the macro scale is a powerful tool for small batch production or larger individual pieces, either of which the Origin One is ready to handle. Additionally, the machine has incredible resolution on the micro-scale, too. Capable of printing with 4k resolution (50 micron pixel size specifically) all the way down to 25um layer heights, unbelievable print results are not only possible, but consistently delivered.
The series of lattice cubes presented through this article were selected to exploit this detail and see how well the machine can actually deliver at this scale. The results speak for themselves. The two smaller lattice figures in clear gave my mirrorless camera with macro-lense a workout it couldn't handle very well, lacking in depth of focus. In the end, a newer phone was used for clearer pictures, and I'm flattered. The machine has performed flawlessly among the many prints I've thrown at it so far. Not immune to print failure, I did get the full experience. However, this time around the failure was in design and promptly highlighted by the print itself. This machine handled every print I threw at it with ease and was a refreshing reminder of what consistent performance feels like. All that's left now is to convince my boss to let me bring it home for "further evaluation!"
Want to learn more about how the Stratasys Origin One can help your research? Contact us today!